Kipp Ivey argues that 3D laser scanning technology will make the circular construction economy possible.
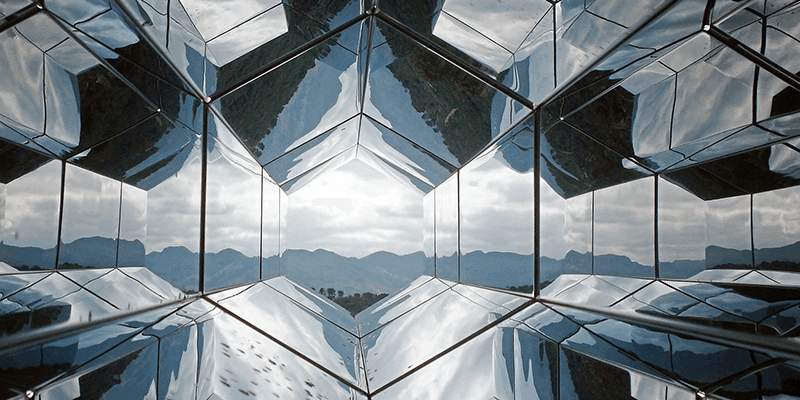
The construction industry is one of the world economy’s most important job-creating sectors. It’s also one of the largest waste generators, with current construction processes responsible for a third of the world’s waste and at least 40% of carbon emissions, according to a European Commission report.
Valuable resources from building demolitions like steel, aluminium, stone and copper often end up in the land fill. Resources aren’t being recovered from these discarded materials and instead are extracted anew from the earth.
This approach can’t last forever. As more countries, cities, and businesses pledge to reach a Net Zero emission output by 2050, the practice of reusing or repurposing construction and demolition waste for retrofits, renovations, or new construction – part of the “circular economy” of using already- available materials in the built environment – is gaining ground. According to a 2020 study by the Club of Rome on Finland, France, the Netherlands, Spain and Sweden, shifting to a more circular construction economy would provide over one million new jobs and cut the carbon emissions of those countries by two-thirds.
One of the biggest ways that construction professionals can work toward this future is by embracing workflows like scan-to-BIM to help eliminate waste and plan for a building’s long- term regenerative future. Essential information is captured as point cloud data using 3D laser scanners or mobile mappers and translated into a BIM output.
A model that’s running on compatible software also usually includes information about thermal performance, electricity, energy emissions and even the impacts that the building has on local wind and weather systems.
Furthermore, BIM is a shared resource – which means that its value extends through the entire life cycle of a building. A major benefit here is total visibility into how construction is progressing against design intent and seeing where repurposed materials can be used with as little waste as possible. This level of accuracy and planning keeps costs and project timelines under control.
During planning and design, laser scanning hardware and modelling software helps with site investigation and surveying – planning a new building that will function symbiotically with its environment. During actual construction, it helps with coordination and saves an incredible amount of time and resources on scrap and rework. Scan-to-BIM is also particularly useful for the maintenance and retrofit stages of a building’s life cycle, as it creates a 100% accurate as-built model of the building to serve as baseline data.
Everyone in the construction industry benefits when the BIM process is used – from urban planners, civil engineers, architects, surveyors, down to the people who will live in or use these buildings a generation from now.
With the amount of waste it reduces, the design foresight it allows, the cross-sector collaboration it enables and the new business it can win for ambitious early adopters, 3D laser scanners and software with scan-to-BIM capability are essential tools that will enable the construction industry to reach the target of Net Zero by 2050.
Kipp Ivey is applications business development manager – AEC, FARO Technologies