Jakub Karas details a project investigating whether UAVs fitted with thermal imaging equipment, cameras and radar could safely
survey power lines in the Czech Republic
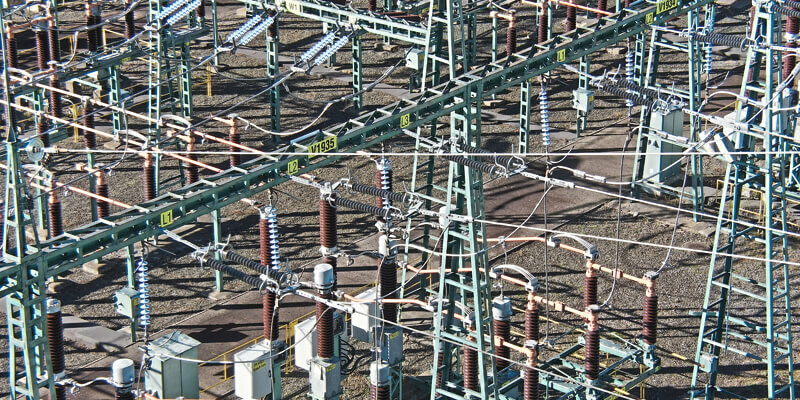
In the autumn of 2021, UpVision conducted a comprehensive project to evaluate the deployment and use of UAVs for the largest electricity system administrator in the Czech Republic.
A pilot project held in 2020 at a test site in the Ore Mountains under the leadership of UpVision and Honeywell had verified the possibility of deploying visual line of sight (VLOS) and beyond visual line of sight (BVLOS) inspections from UAVs on a larger scale in the Czech Republic through this project for inspecting ČEZ Distribuce’s lines.
In this project, tens of kilometres of power lines were selected in the Central Bohemian Region, comprising more than 300 power line poles of different materials, sizes and shapes, including different voltages, and two substations in a variety of different types of environments that may occur within the Czech Republic – fields, meadows, hills, wooded sections, villages and inaccessible sections.
The inspection of the support points was carried out with several types of outputs – RGB and thermo oblique aerial images – and the course of the line and the protection zone was mapped into the resulting high-resolution orthophoto and digital surface model.
Several UAVs such as DJI Phantom 4 Pro, DJI Matrice 600 Pro and DJI Matrice 300 RTK were used for inspection and data collection.
Based on the tests carried out in the pilot project in the Ore Mountains, there was a need to use UAVs with long range and battery life, which is the domain of the new DJI Matrice 300 UAV with RTK and having an RGB sensor and a thermal camera integrated into one sensor H20T with 23x optical zoom. For the most efficient flying around poles, ensuring safety and the possibility of operating the UAV, it was necessary to have a camera that allows a large zoom of the details of the poles from an oblique view from above and without necessarily moving the UAV within the protection zone.
In addition to the optical sensors monitoring the environment for possible obstacle avoidance, this UAV also has a radar located on top that can identify even thin wires of power lines and thus always stop the UAV automatically in time according to the safety limit settings.
Automatic flight plans were created for mapping power line protection zones, where the selected UAV mapped the protection zone of the defined power lines with respect to the terrain situation, most often at an image resolution of 3-5cm/px to create a high image resolution orthophoto and digital surface model.
For the inspection of the poles, the UAV operator was always a two-person team consisting of the UAV pilot and the operator who took the inspection outputs.
A zooming RGB camera in high resolution mode was always used for the image inspection, which recorded the pole from the ground to its top in several tiles. This was done from both sides of the pole, always at a height of several metres obliquely in front of and behind the pole. The number of tiles was always chosen according to the distance of the UAV from the pole and any constraints on the UAV’s approach to the pole and the size of the UAV.
At the same time, the UAV recorded from a closer distance a thermal photo of the top of each pole with insulators. Thermal recording has greater limitations compared to RGB images because it doesn’t allow for zooming, even though the image resolution of the thermal cameras available for UAVs is only 640x512px. This means the UAV needs to be closer to the pole.
Outputs and evaluation
The project showed that it is technically possible for network administrators to carry out inspections by UAV much more efficiently than in previous years. For the purpose of inspecting power lines and poles, it is necessary to have UAVs with RGB sensors with optical zoom at least 5-10x. At the same time, it is advisable to have such a sensor complemented by a thermal sensor within one sensor. Furthermore, it is advisable that the UAV has sensors for obstacle avoidance throughout the body of the UAV, radar for wire detection and other safety features.
In the case of volume measuring of greenery space that encroaches in the protection zone and that will be designated for pruning, for example, it is possible to use photogrammetry. A digital surface model (DSM) in the form of a textured point cloud of tens of millions points per inspection segment is created, from which further profiles can be generated to identify hazardous areas.
The second alternative is to use laser scanning from a UAV, which records vegetation much more accurately and in more detail due to the high density of the scanner recording points per second. Furthermore, the reflectivity of the laser means you can classify different surface types, so you can potentially filter out vegetation and create a digital terrain model directly under this vegetation. However, laser scanners are relatively expensive and heavier for UAVs, resulting in a higher cost; the time required for inspection is also higher than with photogrammetry.
To assess which method you should use to inspect greenery in protection zones, you should take into account the scale and environment of the mapped area and the requirements of the administrator for the accuracy and density of the outputs. At the same time, the two methods can be effectively combined depending on the environment – laser scanning can be used for forest sections, while photogrammetry can be used for most other environments.
Another important validation of the project is that given the size of the acquired data, it is necessary to focus on the efficient cataloguing of only the relevant data, to find defects under the supervision of experts directly from the administrator and to use as much as possible automation based on automatic image analysis for the analysis of all acquired data. This means considerably expanding the library of defects found and their manifestations in the UAV inspection images thus taken, which will serve as the main input for the deployment of automatic image analysis and subsequent defect cataloguing.
On the basis of the inspections carried out, some defects were checked in the field and their identification verified. The comprehensive results are now being evaluated by the administrator and will be used to define the future strategy for this work.
Jakub Karas is director UAS at UpVision