Alexey Dobrovolskiy explains what his company has learned about using UAVs for searching under the surface of the Earth – and the sea – since it accidentally entered the business four years ago, as well as why it has now opened a range for testing new sensors mounted on UAVs
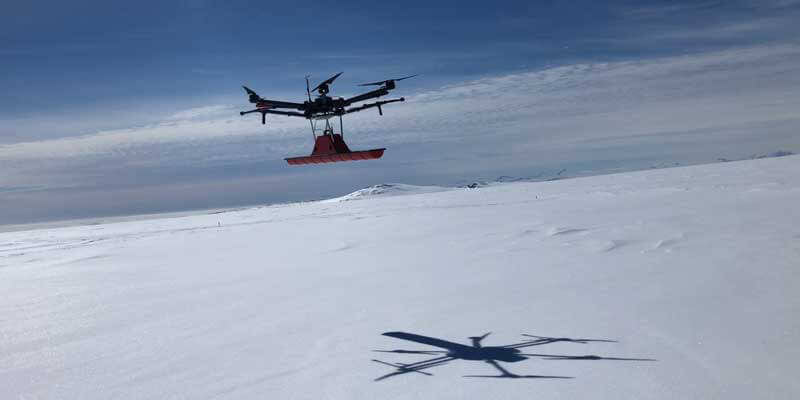
Our integrated sensors business was born on 6 June 2017. That day, our support team received a request from the Fallen American MIA Repatriation Foundation for consultation on how to plan a ground-penetrating radar (GPR) mission for a UAV, with the aim of finding a lost aircraft buried in Greenland’s glacier. At that time, I did not even know what ground-penetrating radar was. Thus, to my surprise I found myself in Greenland – and our company got a new business line.
After the success of the Greenland expedition, we started to receive dozens of requests for GPR and subsurface search. From potential customers, we learned about dozens of possible applications – bathymetry, utilities and archaeology. And since then, we have through our own work learned about and created better ways to search between the surface using UAVs and various sensors.
In Greenland, we used a low-frequency GPR system with very high penetration, but most of the requests we have had are for shallow scanning a few metres underground and for relatively small objects. So, we began by integrating a 500MHz GPR system with a UAV.
But many requests were for the detection of small metallic items – too small for airborne GPR. We therefore made our first attempts at integrating metal detectors with UAVs. Unfortunately, our main disappointment here was the state of the industry of metal detectors – most devices are just toys, and many manufacturers claim absolutely unrealistic detection capabilities. But we learned how to recognise “fake device makers” – if the manufacturer can’t or declines to explain how its device works (in details), it’s better to not deal with it.
We soon found that GPR on a UAV will be just useless in most cases without the ability to keep a constant altitude over surface. So, we developed the first version of a terrain-following system – one that used a laser altimeter.
After delivery of the first dozen GPR systems for UAVs, we started to receive complaints about the terrain-following system when working in different environmental conditions – in fog, over water, ice or snow, and under bright sun. As a result, we redesigned the system and we now supply only systems with radar altimeters for following terrains.
New ways of looking
In 2018-2019, we and our customers gained a lot of experience with freshwater bathymetry using low-frequency GPR. We found that in many cases, there are no alternative solutions to GPR – extreme current and bathymetry through ice are good samples of conditions where GPR is the best solution for bathymetry. Nevertheless, if conditions are close to “normal”, it is better to use an echo sounder – they are cheaper and more precise and data processing is a lot simpler. So, in February last year, we started to work on it, and in March, we announced the first off-the-shelf system with an echo sounder integrated with a UAV.
Last year, we also returned to the idea of an airborne metal detector. This time, we started working with a partner with an extremely good reputation – Geonics, Canada. After a few months of extensive work, we announced a UAV integrated with a special version of the EM61-MK2 metal detector. The benefits compared with magnetometers are simple – EMI metal detectors can detect non-ferrous metals and usually in smaller amounts.
In May, we finished integrating a new, low-frequency system with interchangeable unshielded antennas and started with Radar Systems, Latvia, adapting the system for medium-sized UAVs such as the DJI m300 RTK. There is a strong demand in the market for more compact, light and efficient solutions – and our answer will come soon. That will be the first lightweight GPR airborne system on the market for a wide range of applications.
However, despite the integration of EM61Lite metal detectors, there are still gaps in our capabilities. Imagine that you need to locate a plastic pipe covered by a layer of wet clay. Neither GPR nor a magnetometer or metal detector will be useful in such circumstances.
So, we have started integrating a Geonics EM38-MK2 conductivity meter. Work is still under way, but we have got first results proving applicability of the method.
Testing times
Testing these systems is key and one of things of which I am most proud thus year is our in-house test range. The decision to create a test range arises from an unexpected increase of requests for various integrations with UAVs from potential customers and sensor producers during last year’s pandemic. We have been conducting tests over the range since autumn 2020, but we officially launch our UAV flight test area in spring 2021 to ensure our innovations work properly. The test range is 450m by 70m, and designed for manufacturers, surveying and scientific teams to test their equipment conduct experiments. It allows the testing of various types of geophysical sensor with UAVs.
We considered dozens of real application scenarios when designing the testing area. It has multiple targets of diverse material and size buried in a variety of soils. There are 23 permanently installed targets, such as pipes and barrels, buried in natural soil that has layers ranging from sand to clay, for UAVs to inspect. The coordinates of the targets are known with centimetre-level precision to ensure the highest accuracy for the interpretation of data acquired by the geophysical sensors.
In the first four months of 2021, we sold more airborne GPR systems than in the whole of 2020. It seems that customers’ scepticism towards GPR has finally been overcome.
Alexey Dobrovolskiy is CTO at SPH Engineering (www.ugcs.com)