Chris Thomson explores how, in a first-of-its-kind project, drone technology helped save significant time and money in 3D mapping at Heathrow Airport.
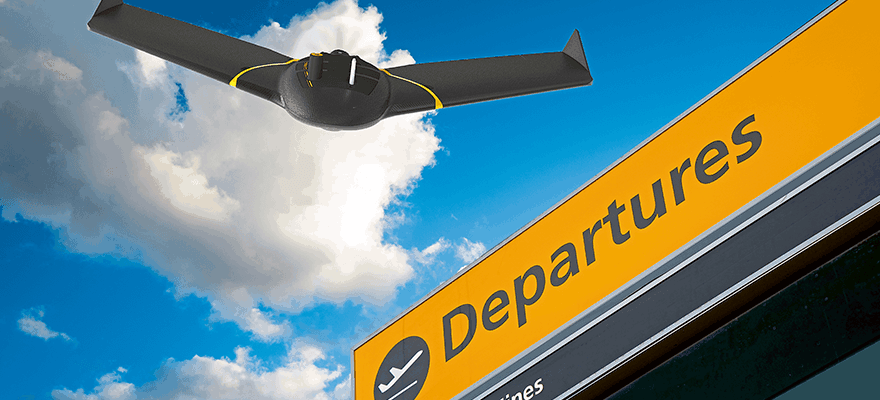
Heathrow Airport is Europe’s busiest airport, and although plans for a third runway are currently on-hold, the expansion will cement its status as a hub for international trade. Already serving more than 80 million passengers a year, another runway would boost the wider economy by up to £61bn and create up to 77,000 local jobs by 2030, according to the UK’s Department for Transport.
As part of its plans for the third runway, Heathrow’s engineering team needed to develop a highly accurate 3D digital model of a 29km2 area surrounding the existing airport. This needed to be conducted quickly and efficiently, without disrupting normal airport operations. The aim was to reduce the amount of time engineers spent on site, minimise downtime, and prevent the project from running late or over budget.
Overcoming barriers
Operating next to a busy airport is a challenging environment for a drone. But the traditional alternative to using drones would not be feasible as much of the surrounding area is privately-owned farmland. With land access restricted, it would be difficult for the team to use ground-based surveying. The large area would also be time-consuming and expensive to map using these traditional methods. Plus, due to the political nature of the project, mapping needed to be completed in a safe and unintrusive way.
Significant planning was required, as mapping would be within Heathrow airspace, up to the boundary fence. The drone and its pilots needed to be able to react quickly to commands from Air Traffic Control (ATC) and put safeguards in place to reduce any risk to Heathrow’s passengers, airlines and staff.
Data processing also posed a potential challenge due to the scale of the site. The last time Heathrow required a data capture of this size, it took almost a year to fully process. Plus, the outputs were restricted to certain members of the team, which limited collaboration and design capabilities. This project for the third runway was different; more data was needed, including engineering-grade measurements, which would then be shared among stakeholders. The Heathrow team, therefore, required a more robust surveying method that provided additional data points.
Which drone is the right drone?
In the first project of this scale, data visualisation specialists Sensat chose to map the area using fixed-wing drones. The team decided to use these, rather than quadcopter platforms, to achieve better coverage on a single flight using only Extended Visual Line of Sight (EVLOS) permissions. By carrying out data capture in a shorter timeframe, it helped minimise interference to other air traffic. It was also important for the chosen drone to be reliable, easy to operate and distinguishable from potential drone threats to the airport.
Sensat has been using senseFly’s eBee system since 2016, and chose to operate its flagship eBee X fixed-wing drone due to its reliability and the company’s trust in the system on similarly high-risk missions around the world. This meant that with the eBee X’s superior endurance and senseFly’s S.O.D.A (a sensor optimised for drone applications and photogrammetry), they could benefit from longer flight times and improved accuracy, with sharper resolution images.
The mission parameters for eBee X were assigned in eMotion, senseFly’s flight planning software, which allows operators to easily set a circular working area as a barrier – preventing entry into restricted zones. By working closely with National Air Traffic Services (NATS), Heathrow Control Tower, Airfield Operations, airport security and the local police forces, Sensat was able to fly unrestricted to capture the necessary data without safety incidents or interruption to normal airport operations.
The mission
After deciding on the drone, the Sensat team used senseFly’s eMotion software to accurately plan, simulate and control operations, while keeping safety firmly in mind. Heathrow provided essential information about the environment, including the different flight areas, which were prioritised and categorised for risk. Maintaining situational awareness was key throughout; the Sensat team used an ADS-B (Automatic Dependent Surveillance- Broadcast) device to monitor all other aircraft coming into land and their proximity, as well as for direct communication with ATC.
Using a fixed-wing drone was a valuable resource-saver. Only two operators were needed for low-risk areas, while a minimum of three people, including a spotter for the runway, were required where the risk was higher. Although there were limitations as to when drone flights could take place, e.g., during certain weeks or parts of the day, the data was captured in just 16 site days – without any need for land access approval.
The results enabled the team to create a high-density point cloud, Digital Surface Models (DSMs), orthomosaic and 3D mesh – totalling 19 billion data points. This information was then shared on Sensat’s cloud-based platform. This provided a collaborative digital native workspace for multiple shareholders. Integrating the data with CAD and BIM also helped to provide more detail, speeding up the design process and reducing the risk for errors. The result: ground-breaking efficiencies leading to a saving £20m and 100,000 project hours.
Future infrastructure plans take off
Using fixed-wing drones was a game-changer for the Heathrow expansion project. It enabled a large area to be surveyed faster and more cost-effectively than typical on-the-ground methods. What’s more, the team could survey the site without gaining land access permissions, which would be lengthy.
The senseFly eBee X proved to be the ideal solution for mapping such a complex, high-risk site. When the expansion plans restart following legal approvals, Sensat plans to use the eBee X again to gather further insights. The data delivered enabled the Heathrow design team to make key strategic decisions with minimal impact on local stakeholders and airport operations. Fixed-wing drones could therefore pave the way for future infrastructure projects of this type –helping design teams across the world achieve significant savings in time and cost.
Chris Thomson is Global Sales Manager at senseFly based in Lausanne, Switzerland (https://www. sensefly.com)