Verification technology can accelerate construction productivity following Covid-19, says Adam Box
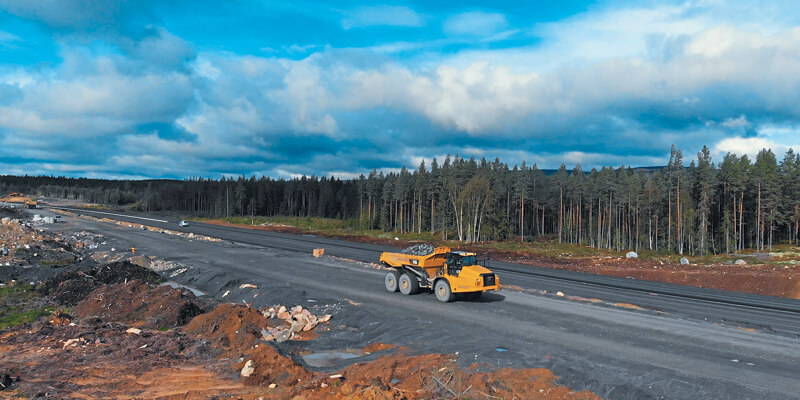
Lockdowns, travel restrictions and site closures led to delays to projects across Europe during 2020. However, given the nature of construction projects and their lengthy planning, financing and execution phases, it’s likely that we won’t feel the full impact of the Covid-19 crisis until much later on. Therefore, it’s imperative that businesses start to put processes in motion that will offset any damage to the industry and help to accelerate economic recovery as swiftly as possible.
The key to this is keeping projects on schedule, meaning it is vital that any potential mistakes or setbacks are identified earlier in the build to avoid expensive problems further down the line. Using technology that can provide a complete record and validation of work, as well as detailed information about any deviations, means costly rework can be avoided and ultimately risks to budgets and schedules can be reduced. The role of this technology in boosting productivity on the construction site has never been more important.
Adapting to the ‘new normal’
Recent research at six major construction schemes suggests that Covid-19 and the ‘new normal’ it’s spawned could actually boost site productivity. Task planning is more detailed, there’s been a boost in the use of technological solutions and increased space has reduced the “overlap” of trades. With social distancing measures in place and fewer workers on site, projects are turning to innovative technologies that might otherwise have taken several years to embed.
Construction verification technology plays an important role in boosting productivity on the construction site. Project teams can account for and adapt to unanticipated design variations almost instantly, and as the data is continuous and real-time, all the members of the team are aware of any changes and updates, revolutionising efficiencies. Not only does this avoid expensive rework further down the line, it also reduces waste from additional reconstruction and workforce time and increases resource savings.
In reality, for verification technology to be powerful, it needs to be active constantly, and this is made possible by empowering those already on-site to capture, monitor and interpret the data themselves. Many construction firms have chosen to outsource the equipment and expertise to third-party scanning teams rather than invest in the technology themselves, due to the upfront investment and time needed for training. But although outsourcing may seem like a more cost-effective alternative, it often means scans are infrequent and, as a result, data quickly becomes old, errors snowball without anybody noticing and you end up with extortionate remedial work to do. This cost then often far exceeds what it would have done if the firms had adopted verification workflows in-house from the beginning.
With fewer workers now allowed on-site due to social distancing, outsourcing this technology may become less of an option anyway. Companies are therefore looking for easy-to-use technology that can not only embed into their workflows, but also enable multi-tasking on site, especially if this means not having to hire specialists.
For example, by investing in solutions like our GTL-1000, a device that combines a robotic total station and a high-quality laser scanner, construction companies can further help to boost efficiencies. The person operating the equipment doesn’t need to be a surveyor, just a team member measuring the layout, who then needs to just click one extra button to conduct a full scan in the same set-up. This drastically improves efficiencies and reduces the amount of resources needed on-site, while helping with social distancing.
When used with software such as MAGNET and ClearEdge3D Verity, operators can process and analyse 3D point clouds for verification analysis and as-built surveys, using one single instrument at every stage of the project. It is now possible to verify up to 99% of as-built construction accuracy in a fraction of the time it would traditionally take to spot check just 5%. This saves vast amounts of time, enabling projects to keep to schedule, which is especially important after the delays caused by the first wave of the pandemic.
This is a great example of how technology can augment a process, limiting the number of people required on-site, while instilling construction professionals with new, useful skills and capabilities – all while improving productivity and reducing costs.
A full workflow at your fingertips
Workflow technology software such as MAGNET ensures all the solutions being used are working from the same data, meaning that all stakeholders have access to the same information, including reports, in near-real time. With this full project connectivity at your fingertips, collaboration and communication on-site can be revolutionised and accurate data can be seamlessly sent from site to office without the need for additional resources.
On a recent road construction project in Norway, the Skanska team used MAGNET to manage construction work on the country’s biggest road to date, known as Den Grønne Snarvei. The software was also a key factor in Skanska winning the project. Skanska wanted a streamlined digital workflow and MAGNET offers exactly that – users can visualise all project data in one view, evaluating different design options and instantly seeing how they influence the cost, helping to create realistic and accurate project plans. In Norway, the software also helped to optimise cut and fill quantities as well as minimise mass haul distances, while maintaining safety and quality.
Overall, MAGNET helped to reduce planning and construction budgets on the project by 20% and continues to support Skanska and the State Highways Authority in their environmental objectives. It has also helped to significantly reduce the construction period of the project; the road, which was due for completion in late 2020, opened three months early in July.
Talking about the difference MAGNET has made to the project’s efficiency, Lucia Calzado Teruel, a planner for Skanska, said: “You get all the information on mass haul, line-of-balance plans, Gantt charts and reports in one file. Before I started using MAGNET, I needed different files that didn’t work together. MAGNET is much more time-efficient and ensures you deliver high-quality work.”
As we adjust to the changes caused by the Covid-19 pandemic and subsequent lockdowns, verification technology and software that enables an efficient, automated workflow will be crucial in accelerating the industry’s economic recovery. By embracing and adopting these new digital tools, businesses can ensure that they are future-proofed and ready for whatever is around the corner.
Adam Box is business development manager vertical construction at Topcon Positioning Group