An indoor positioning technology originally developed for use with cars IS finding applications in other sectors, including construction. Jennifer Edis looks at how it works and what the challenges were in adapting it
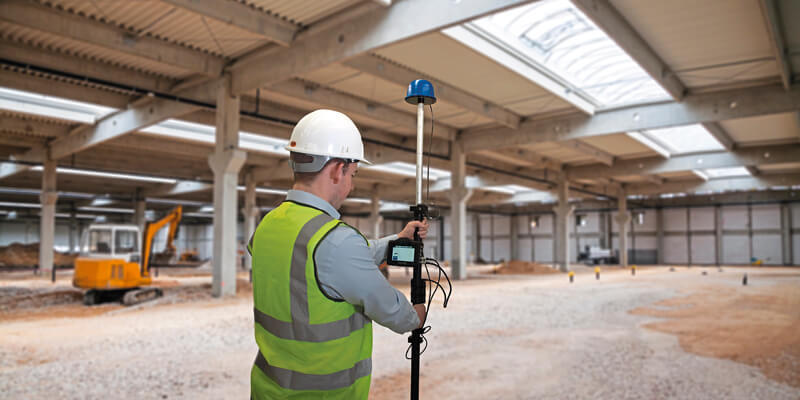
The advent of the use of GPS technology for testing and control has delivered unprecedented accuracy in the measurement of speed and position. Applications involving a moving target benefit from the high dynamic capabilities that have driven technological advances in sectors including automotive, mining and construction.
However, the reliance on GPS transfers its limitations to any technology into which it is integrated. The most common problem encountered is loss of satellite signal when a clear line of sight to the sky is restricted because the receiver is indoors, underground, in an urban canyon, or obscured by natural or manmade obstacles such as dense tree coverage or passing under a bridge.
Positioning technology has adapted over time to meet the demands of many sectors craving the capabilities of GPS in such environments. Indoor positioning for high volume location and tracking is commonplace in warehousing, logistics, and tracking people and goods. With relatively low speed, dynamics and accuracy, it is scalable and integrates well with other automated systems.
However, the demands of other sectors have posed more of a challenge to indoor positioning systems (IPS). Automotive applications require centimetre accuracy at high speeds with seamless transition from GPS to IPS. Autonomous vehicle control has equal requirements with the addition of operating in large and, in the case of mining and tunnelling, often hostile environments. Construction is perhaps the most demanding sector of all, requiring all these capabilities combined with the need for a flexible and transferable installation due to the variety and relative short-term operation of sites.
Open air construction has reaped the benefits of GPS technology, but the sector has been somewhat neglected when it comes to IPS. My company, Racelogic, which previously specialised in the automotive market, recently launched a new indoor positioning system called VIPS (VBOX Indoor Positioning System), which we believe offers a solution that will provide the construction industry with an accurate, affordable and adaptable IPS to bring GPS technology to any construction site.
However, indoor positioning systems are not a novel technology, so what is different about VIPS and why does Racelogic believe it is ideal for applications in the construction industry?
Construction challenges
The challenges faced by IPS have been met with a range of technology solutions, each with its own strengths and target applications. Networks of ground-based transmitters offer a significant solution for large-scale radio-positioning. With autonomous synchronisation of terrestrial transceivers, they deliver highly accurate, completely autonomous position solutions for high-end applications including the military. Ultra-wideband (UWB) beacon systems use base stations, reference transponders and external computing power to deliver 5cm accuracy. These are commonly used for transport applications with permanent installations for rail positioning and portable systems for automotive testing, which when combined with an inertial measurement unit (IMU) can bring accuracy closer to 3cm.
Whilst these solutions are effective, they have limitations. Cost-benefit ratios can be prohibitive if the robust level of accuracy is beyond what is required or, in the case of construction, if the installation is not permanent. The prerequisite of large amounts of hardware including base stations, bespoke receivers, reference stations and processing computers not only has cost implications, but the complexity can impede integration with other systems.
Additionally, solutions that have been developed for a singular application can make transitioning or integrating with other applications convoluted. The time and difficulty level of installation can be limiting for applications where sites are not permanent or for facilities with multiple locations. And finally, there is the simple issue of cost. Limited budgets can make solutions unfeasible or push the price of an integrated product beyond a realistic price point.
When devising a solution that overcomes these limitations, we evaluated several existing technologies. WiFi and other non-UWB radio signals are cost-effective and proven technologies, but are generally inaccurate due to their reliance on signal strength rather than time of flight. Optical systems present the opposite evaluation, with high accuracy at the expense of high costs. They generally also require a large amount of calibration and can be fragile in challenging environments, as the system can lose lock and struggle with reacquisition if the target passes behind an obstacle.
Conventional UWB, while a proven technology in warehouse and similar applications involving the tracking of a large number of slow-moving tags and easily modifiable to track a smaller number of items at a higher rate, still retains a centralised structure requiring data communications and time synchronisation to all of the in-building infrastructure. Additionally, the use of a central computer to calculate locations leads to larger and often variable latency of the position data at the target.
Intelligence on the move
The base technology we selected to develop VIPS was UWB, due to the positive balance of cost and performance for indoor applications. However, as detailed above, a conventional warehouse style system has significant limitations regarding the infrastructure around the test area.
To overcome these limitations, the intelligence of the VIPS system is housed in the mobile unit on the target, thus allowing the rest of the system to be simplified and removing the need for any special cabling or timing synchronisation between the in-building equipment. The fixed structure only requires power, and for short term installations this can easily be supplied via small battery packs.
In addition to simplifying the installation and setup process, this on target approach allows the system to operate with a low and constant latency in the position output, something that is critical for many machine control type applications that have come to expect this from GPS position sources.
As a result, VIPS delivers better than 2cm accuracy with an update rate of 100 times a second, making it ideal for dynamic applications. The level of accuracy is maintained with seamless transition from GPS to VIPS with reacquisition in less than 0.2 seconds.
VIPS delivers this performance by using a network of independent beacons placed around the perimeter of the operation area – for example, the floor plan of a building or construction site – in known positions that have been manually surveyed using a handheld laser, total station or, if time is of the essence, a self-survey. A full VIPS system can be deployed in 25 minutes and provide 2cm accurate positions immediately. The small size of the beacons makes installation possible in almost any environment and its portability lends itself to multiple usage locations.
A UWB receiver on the target object communicates with the beacons and uses trilateration to determine its position. This data is combined with the measurements from a highly accurate inertial measurement system, providing real-time, 3D position to within 2cm, including the option to output attitude, pitch (±0.1°), roll (±0.1°) and heading (±0.5°).
Taking learning from cars to construction
In line with Racelogic’s automotive heritage, VIPS was initially developed for the automotive testing market. However, it was essential that it was flexible in its design and range of potential applications so that it overcame many of the limitations of existing systems.
When considering construction applications, the level of performance delivered by VIPS was undoubtedly a priority, but this had to be combined with other capabilities specific to the needs of the construction industry. Its ease of set-up and non-permanent installation options means that it does not add excessive time to project plans and can be transferred between sites. It is also adaptable, so that integration with other technology and machinery is simple, with flexibility to allow for bespoke integrations. Perhaps most importantly, it is affordable, and it is the price point that has seen VIPS generate interest from a diverse range of customers.
VIPS and its sister technology VPRS (VBOX Precision Ranging System) are being developed for applications including indoor/outdoor surveys, snagging, AR, machine control, crane safety, depth measurement and automated guided vehicles. It is already being used in the drilling of foundations in a dense urban construction site in San Francisco, in the US.
The simplicity of its installation and use, paired with high performance accuracy also makes VIPS attractive to systems integrators. Optical tracking systems are starting to reduce in price to the point where they are now becoming practical for many applications. However, they still suffer from the fragility previously mentioned in that once lock is lost on a target, they can take a significant amount of time to re-acquire it. This is especially true if the target is moving at the time. Using multiple tracking systems is a viable solution but it re-establishes the issue of prohibitive pricing.
Combining the affordability and performance of VIPS with this new generation of robotic optical systems has other benefits. The optical system can further increase the speed of the VIPS set-up process and once in place, VIPS provides an effective partner to the optical system. If the more accurate optical system does lose position it can reference the VIPS provided location and use it to seed the optical tracking system, greatly reducing the reacquisition time. If also combined with an inertial system to smooth the transitions between VIPS and optical positioning, the final output can maintain optical quality position even in environments where line of sight to the optical system is frequently obscured.
Jennifer Edis is brand marketing manager at Racelogic (www.racelogic.co.uk)